The differences between complex single and multi-engine props
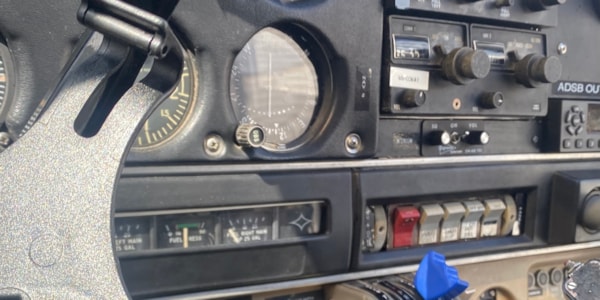
What type of aircraft did you do your complex training in? A single-engine or multi-engine? Whatever type of aircraft you did it in, you at some point had to learn about the prop system and how it operated. All complex props are the same right? Let’s review the basics of the prop system and how it changes from one engine to two.
Both types of constant-speed props use a governor to control the RPM of the engine. The governor is able to maintain control with the help of mechanical linkages connected to the propeller control knob/lever to a speeder spring, centrifugal flyweights, and a pilot valve with allows the flow of oil to move either to or from the oil sump. Changing the RPM of the engine and the pitch of the propeller blades allows for better performance and fuel efficiency during different phases of flight. For example, Takeoff or cruise.
Without going into all of the details regarding how the prop works, the main difference between the single-engine and the multi-engine complex prop— is the oil pressure movement. Similar to both systems, as you begin pulling the prop lever back, you are adjusting the prop to take bigger ‘bites’ of air. What that means is, that you’re increasing the angle-of-attack of the propeller.
Photo create Wikipedia.com
Which direction is the oil flowing? Unlike single-engine constant speed props, the majority of twin-engine constant speed props require oil pressure to drive the propellers toward High RPM, and low pitch (unfeathered). They are also equipped with a nitrogen charge and spring to drive the propeller toward Low RPM, high pitch (feathered). The oil flows out of the prop hub back into the oil sump. A single-engine prop acts opposite to this meaning the oil pressure would drive it to a low RPM, high pitch.
Why is this? The way these two systems are engineered is all due to performance in the event of an oil pressure loss. If you lose oil pressure in a multi-engine the prop will move towards the high pitch, low RPM feathered position to avoid a windmilling propeller and asymmetrical thrust. By losing 50% of your power during an engine failure in a twin, you consequently lose roughly 80% of your performance.
Most single-engine constant speed propellers are designed to ‘fail forward’, meaning if engine oil runs out or fails, the propeller will automatically move into the low pitch/high RPM setting. You will still have a reduction in performance with the windmilling prop, just not an issue with the asymmetrical thrust creating less rudder effectiveness.
Please leave any questions or comments below!
Recent Comments